Hiwin Controller and Drive - E1 series
The universal design, supporting AC servo motor, linear motor and direct drive motor, meets the application needs of various industries.
Controller and Drive - E1 series
The intelligent tuneless function can easily handle mechanism with different load changes, make the machine operate fast and stably, and effectively shorten the setup time. The evolving auto tune function can help the machine achieve its best performance. With 3.2kHz speed bandwidth, the productivity of the stage can be greatly increased. The excellent performance of the unique gantry control function provides users a high performance and more cost-effective solution for control system.
ดาวน์โหลดไฟล์ PDF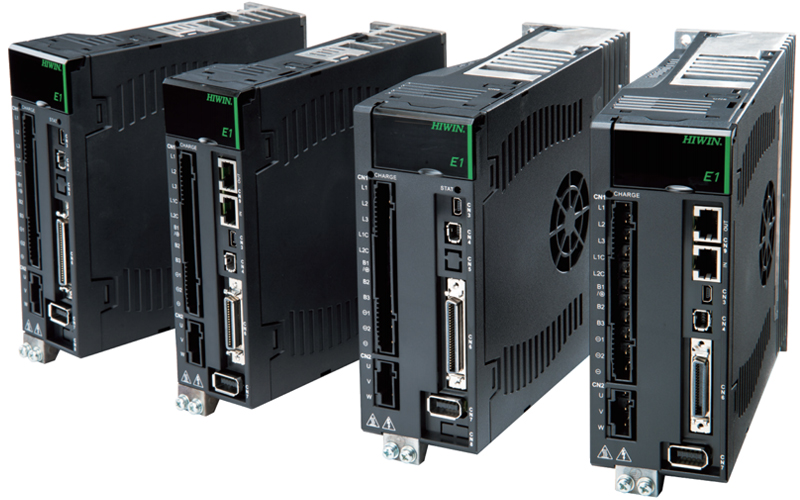
Feature | Controller and Drive - E1 series
- 200-240VAC power input
- Support Functional Safety: STO function
- Support three types of pulse signal (A/B, Pulse/dir, CW/CCW) for command input
- With two independent channels of 16-bit high-resolution analog voltage command input, suitable for velocity control mode and torque control mode
- Support standard EtherCAT and MECHATROLINKIII high speed communication interface
- Built-in velocity ripple compensation, vibration suppression and error compensation
Code | Controller and Drive - E1 series
Dimensions | Controller and Drive - E1 series
Specifications | Controller and Drive - E1 series
ตารางสเปค 1 (Specification 1)
Rated Output | 400W | 1KW | 2KW |
---|---|---|---|
Rated Voltage (line to line) | AC 200~240 Vrms 50~60Hz | ||
Phase Voltage of Main Power (line to line) | 1 Ø/AC 200~240 Vrms | 3 Ø/AC 200~240 Vrms | |
3 Ø/AC 200~240 Vrms | |||
Current (Arms) | 1.5 | 5 | 11.3 |
Current (A-amp) | 2.1 | 7.1 | 15.98 |
Cnotrol Power | 1 Ø/AC 90~240 V, 50~60 Hz | ||
Phase Voltage | 3 Ø/AC 240 Vrms | ||
Rated Power (W) | 400 | 1K | 2K |
Peak Current (Arms) / [A-amp] | 10/14.1 | 23.3/33 | 42/59.4 |
Rated Current (Arms) | 2.5 | 5.6 | 12 |
Frame | B | C | D |
Cooling method | Fan cooling | ||
Control Method | IGBT PWM spec vector control | ||
PWM Modulation Frequency | 16 KHz | 8Hz | |
Applicable Motor | AC/DM/LM | ||
STAT LED Indicator | Red: Error / Green:Servo ready | ||
CHARGE LED Indicator | Red: Control power is turned on. / No light: Control power is not supplied. | ||
Built-in Regenerative Resistor | - | 40 Ohm / 40 W | 12 Ohn / 60 W |
Dynamic Nrake | Built-in dynamic brake / Delay time of relay: 20 ms | ||
Internal Dynamic Brake Resistor | - | 10 Ohm | |
Analog Output | Channel: 2 / Resolution: 12 bit / Output voltage range: ±10V / Accuracy: ±2% / Max. output current: ±10mA | ||
Control Function | |||
Position Mode | |||
Command Source | Pulse command from controller | ||
Signal Type | Pulse / Direction, CW / CCW, A/B phase | ||
Isolated Circuit | High-speed photo coupler | ||
Input Signal | Differential input or single-ended: 200 kpps | ||
Electronic Gear | Gear ratio: pulses Counts, PulseL 1~1,073,741,824, Counts: 1~1,073,741,824 | ||
Velecity Mode Analog Input | |||
Command Source | DC voltage command from controller | ||
Impedance | 14K Ohm | ||
Signal Format | ±10Vdc | ||
Max. input Bandwidth | 100 Hz | ||
Specification | 16 bit A/D input (V-REF+/-) | ||
Torque Mode Analog Input | |||
Command Source | DC voltage command from controller | ||
Impedance | 14K Ohm | ||
Singal Format | ±10 Vdc | ||
Max. Input Bandwidth | 100 Hz | ||
Specification | 16 A / D input (T-REF+/-) |
ตารางสเปค 2 (Specification 2)
Rated Output | 400W | 1KW | 2KW |
---|---|---|---|
Control Mode | - Position mode - Velocity mode - Torque mode - Full closed loop mode (Due loop mode) |
||
Power Supply | ±5.1 Vdc±5%, 400mA | ||
Singal Format | Serial signal - Resolution: 23 bit (Single-turn / multiturn absolute encoder) Bandwidth: 5 MHz Incremental signal - AqB and Z phase signals (Digital differentail TTL signal) The maimum input bandwidth of each phase is 5 MHz. | ||
Safety Fucntion | Encoder power malfunction detection / Short circuit protection / Undervoltage protection / Overvoltage protection | ||
Position Counting Range | -2,147,483,648~2,147,483,647 (32 bit) | ||
Max. Bandwidth of Differential Input | Full closed loop (Quadruple frequency, 20 M counts/s) | ||
Linear Motor / Torque Motor | Encoder smart cube (ESC)must be connected, depending on encoder type. | ||
Z Phase |
|
||
A/B phase |
|
||
Computer Communication Standard USB2.0 (Mini USB type) | Connect the servo drive with your computer to set parameters, monitor physical quentities and execute trial operations via Thunder. | ||
Inout | The function of general -purpose inputs (I1~I10, photocoupler) can be defined by user. 24 V/5 mA (Each input pin) | ||
Output | The function of general-purpose output s (O1~O5, photocouler) can be defind by user. 24 V/0.1 A (Each output pin) | ||
Position Trigger (PT) | Differential signal output. It is configured and activated by parameters. | ||
Regenerative Resistor | +HV > 380 Vdc | ||
Protection of Regenerative Resistor Disabled | +HV < 370 Vdc | ||
Tolerance | ±5% | ||
Optional Function | Gentry control | ||
Insulation Voltage | Impedance between main power and ground is 1,500 Vac. (A minute) | ||
Operating Temperature | 0~45°C | ||
Storage Temperature | -20~60°C | ||
Humidity | Operating and storage temperature: 20 to 85%RH (Non-condensing) | ||
Altitude | Altitude 1,000 M or lower above sea level | ||
Vibrating | Less than 5.88m/s2 10 to 60Hz | ||
IP Rating | IP20 |